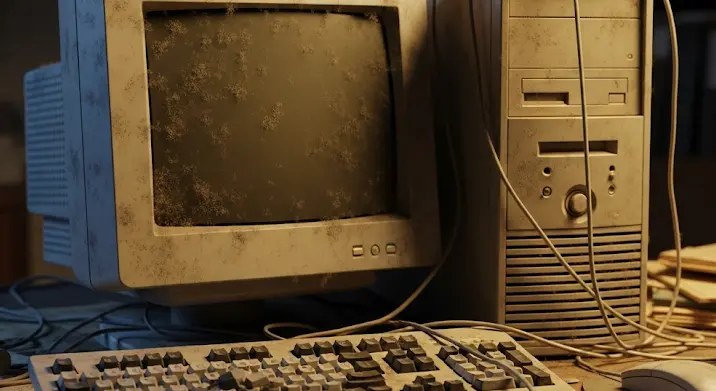
Egy ipari gép működése során a teljesítménycsökkenés az egyik legfrusztrálóbb és legköltségesebb probléma, amellyel egy üzem szembesülhet. Nem csupán a termelékenységet veti vissza, hanem a minőség romlásához, a selejt mennyiségének növekedéséhez és végső soron jelentős pénzügyi veszteségekhez vezethet. Amikor egy gép már nem képes a gyári specifikációk szerint, vagy a korábbi ütemben dolgozni, sürgősen fel kell deríteni a probléma gyökerét. De mi okozza valójában a teljesítményvesztést, és milyen jelekre figyeljünk oda? Ez a cikk részletesen elemzi a gép teljesítménycsökkenésének leggyakoribb okait, és iránymutatást ad a megelőzéshez és a hatékony hibaelhárításhoz.
A Teljesítménycsökkenés Tünetei és Hatásai
Mielőtt mélyebben beleásnánk magunkat az okokba, fontos felismerni a tüneteket. A gép teljesítménycsökkenés jelei lehetnek a lassabb ciklusidő, a megnövekedett energiafogyasztás, a gyakori leállások, a melegedés, a szokatlan zajok, a pontosság romlása, vagy éppen a megnövekedett selejtarány. Ezen jelek figyelmen kívül hagyása súlyosabb meghibásodásokhoz és drágább javításokhoz vezethet, vagy akár az egész gyártósor leállását is okozhatja. A cél mindig a proaktív felismerés és a gyors beavatkozás kell, hogy legyen.
A Teljesítménycsökkenés Főbb Okai: Részletes Analízis
1. Mechanikai Kopás és Hiba
A gépekben lévő mozgó alkatrészek folyamatos súrlódásnak és terhelésnek vannak kitéve, ami elkerülhetetlenül mechanikai kopáshoz vezet. Ez az egyik leggyakoribb ok. A csapágyak elhasználódása például megnövekedett súrlódást, hőtermelést és pontatlanságot okozhat, ami jelentősen befolyásolja a gép működési sebességét és pontosságát. A fogaskerekek kopása, a hidraulikus rendszerek szivárgása, a tömítések elöregedése, vagy éppen a nem megfelelő kenés mind hozzájárulhatnak a teljesítményromláshoz. A túlterhelés, a nem megfelelő illesztés, vagy a gyenge minőségű alkatrészek szintén gyorsíthatják a kopási folyamatot. A periodikus gépmegfigyelés és a kopó alkatrészek időben történő cseréje kulcsfontosságú a megelőzésben.
2. Elektromos és Elektronikai Problémák
A modern ipari gépek komplex elektromos és elektronikai rendszerekre épülnek. Egy meghibásodott motor, egy hibás érzékelő, egy sérült kábelezés vagy egy túlfeszültség okozta károsodás mind elektromos probléma forrása lehet. A motorok teljesítményvesztése, a szenzorok pontatlan adatgyűjtése, a relék beragadása, vagy a vezérlőpanelek hibái közvetlenül befolyásolhatják a gép működési ciklusát és hatékonyságát. A laza csatlakozások, az oxidáció, a rövidzárlatok, vagy a túlzott feszültségingadozások mind észrevétlen, de romboló hatással lehetnek. Az elektromos diagnosztika és a rendszeres ellenőrzések elengedhetetlenek a rejtett hibák felderítéséhez.
3. Szoftveres és Vezérlőrendszeri Gondok
Egyre több gép működését vezérlik PLC-k (programozható logikai vezérlők) és komplex szoftverek. A szoftveres hibák, mint például egy hibás algoritmus, egy programozási tévedés, vagy egy elavult firmware verzió, súlyos teljesítménycsökkenéshez vezethetnek. A kalibrációs problémák, a kommunikációs zavarok a különböző komponensek között, vagy a hálózati késleltetések szintén lelassíthatják a gép működését, vagy pontatlan végrehajtást eredményezhetnek. Egy nem megfelelően végrehajtott szoftverfrissítés is okozhat kompatibilitási problémákat. Az ipari automatizálás ezen területe különös figyelmet igényel, a rendszeres szoftveres karbantartás és a vezérlőrendszerek naprakészen tartása kulcsfontosságú.
4. Környezeti Tényezők Hatása
A gép működési környezete is jelentősen befolyásolhatja a teljesítményét. A szélsőséges hőmérséklet (akár túl magas, akár túl alacsony), a magas páratartalom, a por, a szennyeződések, vagy a túlzott vibráció mind hozzájárulhatnak a meghibásodáshoz és a teljesítményromláshoz. A por és a szennyeződések eltömíthetik a szűrőket, lerakódhatnak az érzékeny elektronikai alkatrészeken, vagy növelhetik a mozgó alkatrészek súrlódását. A magas páratartalom korróziót okozhat az elektromos csatlakozásokon, míg a túlzott vibráció a mechanikai kötések lazulásához és az alkatrészek idő előtti kopásához vezethet. A megfelelő üzemeltetési környezet biztosítása alapvető a hosszú távú, stabil működéshez.
5. Karbantartási Hiányosságok
Talán az egyik leggyakoribb és elkerülhető ok a nem megfelelő vagy elmaradó karbantartás. Az ütemezett megelőző karbantartás hiánya, az olajcserék elmulasztása, a szűrők tisztításának vagy cseréjének elhanyagolása mind-mind felgyorsítja a kopást és a hibák megjelenését. A nem szakszerű javítások, az eredeti alkatrészek helyett gyenge minőségű, utángyártott alkatrészek beépítése, vagy a nem megfelelő kenőanyagok használata szintén rövidítheti a gép élettartamát és ronthatja a teljesítményét. Az előrejelző karbantartás bevezetése, amely szenzorok és adatelemzés segítségével azonosítja a potenciális problémákat még azok bekövetkezése előtt, jelentős mértékben javíthatja a gépek rendelkezésre állását és teljesítményét.
6. Emberi Hiba és Helytelen Üzemeltetés
Bár a gépek önállóan dolgoznak, az emberi tényező továbbra is kritikus. A gép nem megfelelő beállítása, túlterhelése, az előírt működési paraméterek figyelmen kívül hagyása, vagy a szakképzetlen személyzet általi kezelés mind operátori hiba forrása lehet. A nem elegendő képzés, a biztonsági protokollok be nem tartása, vagy a rutinszerű ellenőrzések elmaradása mind hozzájárulhat a teljesítményromláshoz vagy a váratlan meghibásodásokhoz. A megfelelő képzés, a világos üzemeltetési útmutatók és a rendszeres felügyelet elengedhetetlen a hatékony és biztonságos működéshez.
7. Alapanyag Minősége és Feldolgozási Kihívások
Gyakran figyelmen kívül hagyott tényező az alapanyag minősége. Ha a gép rossz minőségű, inkonzisztens vagy nem a specifikációnak megfelelő alapanyaggal dolgozik, az ronthatja a gép teljesítményét. Az eltérő keménység, szennyeződések, vagy méretpontatlanságok megnövelhetik a gép terhelését, gyorsíthatják a kopást, vagy akár hibás termékek gyártásához is vezethetnek, ami végső soron a gép kihasználtságát és hatékonyságát rontja. Az anyagminőség ellenőrzése létfontosságú.
8. Elöregedés és Tervezési Korlátok
Végül, de nem utolsósorban, minden gépnek van egy tervezett élettartama. Az elöregedés természetes folyamat, amely során az alkatrészek anyaga fárad, elveszti eredeti tulajdonságait, és a gép hatékonysága csökken. Bizonyos esetekben a gép alapvető tervezési korlátai is okozhatnak teljesítményproblémákat, különösen, ha a gyártási igények növekednek, vagy a technológia fejlődésével új standardok jelennek meg. Ilyenkor érdemes megfontolni a modernizációt vagy egy új berendezés beszerzését.
Megoldások és Megelőzési Stratégiák
A teljesítménycsökkenés megelőzése sokkal költséghatékonyabb, mint a javítás. A legfontosabb stratégia a proaktív karbantartás, beleértve a rendszeres ellenőrzéseket, a kenőanyagok cseréjét, a kopó alkatrészek előre tervezett cseréjét és a szoftverfrissítéseket. A szenzoralapú állapotfelügyelet (condition monitoring) és az adatelemzés lehetővé teszi a problémák korai felismerését, mielőtt azok súlyosabbá válnának. A személyzet megfelelő képzése, az üzemeltetési protokollok szigorú betartása és a tiszta, stabil üzemeltetési környezet biztosítása szintén elengedhetetlen. A beruházás minőségi alkatrészekbe és a legújabb technológiákba hosszú távon megtérülő befektetés.
Összegzés
A gép teljesítménycsökkenése összetett probléma, amelynek számos oka lehet, a mechanikai kopástól az elektronikai hibákon át a szoftveres problémákig és az emberi tényezőig. A gyors és hatékony hibaelhárítás, valamint a proaktív gép karbantartás kulcsfontosságú a termelékenység fenntartásához és az üzemi költségek minimalizálásához. Az okok mélyreható megértése és a megfelelő megelőző intézkedések bevezetése biztosítja, hogy gépei a lehető leghosszabb ideig optimális teljesítménnyel működjenek, garantálva ezzel a sikeres és gazdaságos termelést.